本文介绍了 LED 产品做智能化升级时对 LED 驱动电源开发过程需要了解的相关信息。
背景信息
LED 产品智能化就是在传统 LED 驱动设计的基础上,嵌入无线组件(Wi-Fi、Zigbee、BLE 等),扩展 LED 产品调光,调色,远程控制和智能联动功能。因此,设计时,需要考虑在满足 LED 正常工作的电源基础上,增加无线组件的电源需求。
方案框图
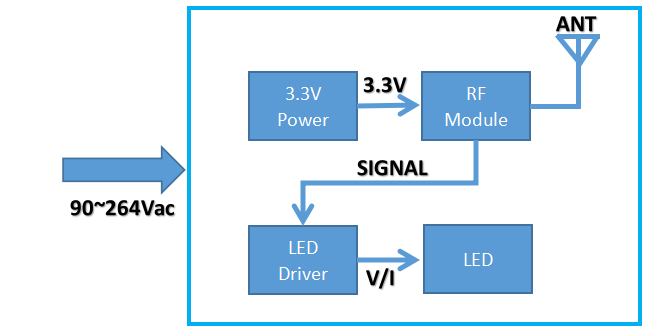
第一步 选择 RF 模组供电方案
RF 模组的功耗具有瞬时电流峰值高,平均电流相对小的特点。因此在选择模组的供电方案时,需要详细查看模组规格书中的平均电流值和瞬时电流值。以下罗列了几种 RF 模组供电方案。
AC-DC恒压输出供电
模组供电电源直接从高压端(VBUS)经过 AC-DC 恒压芯片转换输出稳定 3.3V 电压供模组使用。
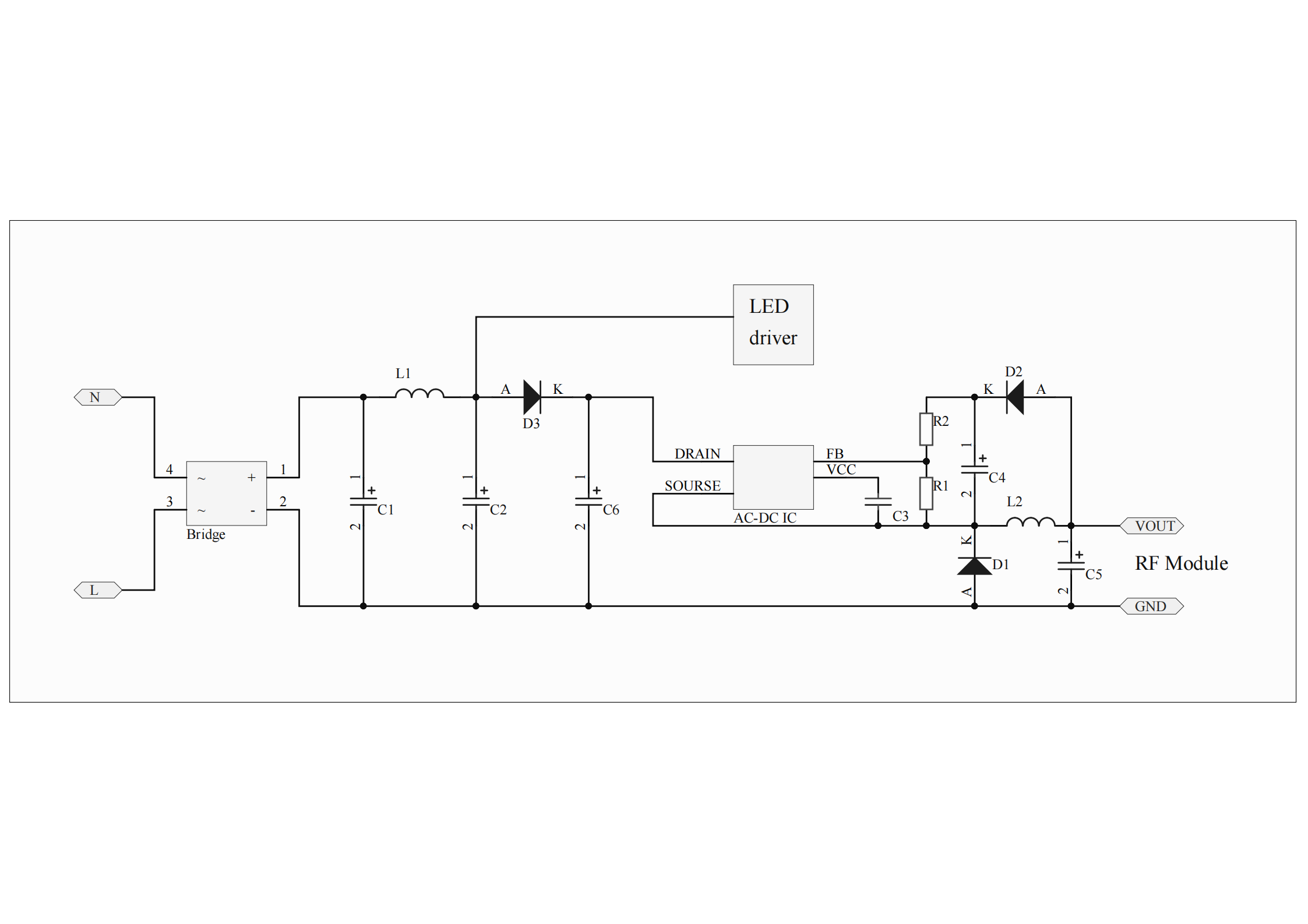
设计注意事项
-
AC-DC 供电电路需使用二极管加电容来与 LED 驱动部分隔离,防止模组在工作时对主功率部分产生影响。特别是线性恒流驱动电源,需要做隔离来避免出现灯光抖动现象。
-
输出电压纹波小于 100mV。防止输出平均电压叠加上纹波后,电压超过或低于模组工作电压限值。
-
AC-DC 电源方案需具有输出平均电流能力不小于 RF 模组各状态下最大平均电流值的两倍,且电源输出动态电流能力满足模组瞬态峰值电流值的需求。以下是各 RF 模组的 AC-DC 电源推荐参数:
RF 模组 |
电源输出平均电流值 |
电源动态电流最大值 |
Wi-Fi 模组 |
200mA/3.3V |
450mA |
BLE 模组 |
50mA/3.3V |
100mA |
Zigbee 模组 |
50mA/3.3V |
100mA |
-
母线电压端的电解电容总容量选择需要根据灯驱动的负载和 RF 模组的负载的累积。
-
在低待机功耗应用场合,需选择低待机功耗 AC-DC 驱动芯片,配合使用低待机电流的模组。
-
AC-DC 恒压电路设计可参考 电源设计 文档,了解相关注意点。
DC-DC 恒压输出供电
模组供电电源直接 LED 驱动后级低压恒压端口取电,经过 DC-DC 恒压芯片转换输出稳定 3.3V 电压供模组使用。该方案主要应用在 5 路 LED 灯具上。
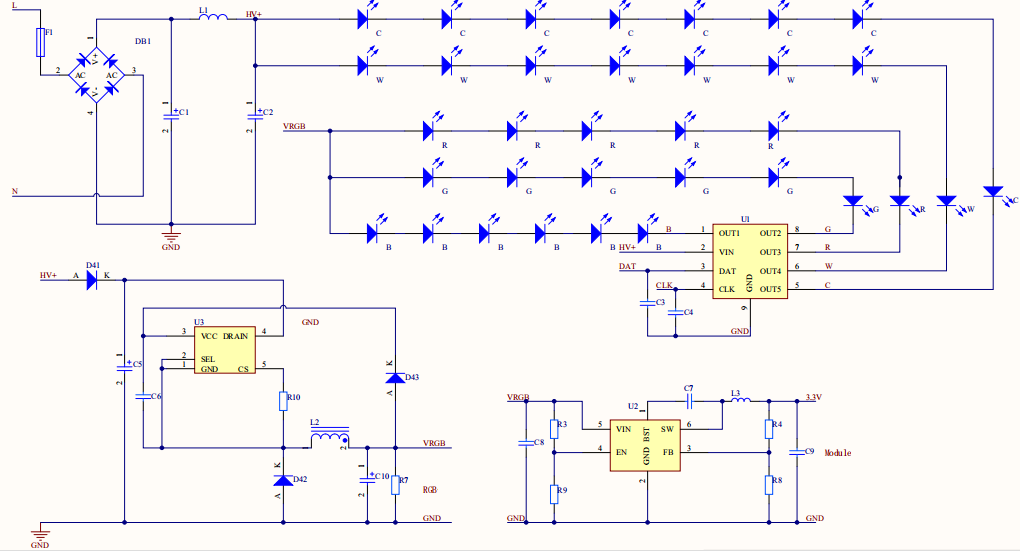
设计注意事项
- 当 LED 驱动后级低压恒压端口电压超过 12V 时,不推荐使用 LDO 降压至 3.3V 给模组使用,可使用 DC-DC 转换芯片降压至 3.3V。DC-DC 电源方案需具有输出平均电流能力不小于 RF 模组各状态下最大平均电流值的两倍,且电源输出动态电流能力满足模组瞬态峰值电流值的需求。各类型 RF 模组对电源的需求可参考上表。
- 不推荐使用 LDO 供电给 Wi-Fi 模组有些限制。如果使用 LDO,则需要选用供电电流 500mA 及以上的芯片,同时需要注意散热。
- 使用 LDO 时,需要注意 LDO 工作的功耗,LDO 功耗的计算是 LDO 前后级的压差乘以流过的电流值。压差越高,LDO 的功耗越大。还需要注意 LDO 的最大电流值是否满足模组的峰值电流值。当模组的峰值电流值顶到 LDO 的最大电流值,可能会引起 LDO 保护,导致输出电压塌陷,使模组不正常工作。
- 基于 DC-DC 转换芯片设计的 Buck 电路,需要注意两个主功率环路面积尽量小。
- 环路 1:C8 正极 > U2 > L3 > C9 正极 > C9 负极 > C8 负极。
- 环路 2:U2 SW 引脚 > L3 > C9 正极 > C9 负极 > U2 GND 引脚。
- 基于 DC-DC 转换芯片设计的 Buck 电路,需要注意反馈电阻和芯片引脚的滤波电容都要靠近芯片引脚放置。
当 LED 驱动采纳线性调光方案,且模组是蓝牙或 Zigbee 等低功耗模组时,模组的电源方案
当 LED 驱动选择线性调光方案时,因为灯驱动的效率较高,一般会选择输出电压和输入电压压差较小的方案。当输入电压断电后,输入电解电容的电压低于输出电压时灯灭,输入电容仍有很大残压需要需要通过输入电容假负载和 AC-DC 供电部分来放电(主功率电容容值一般较大)。当选择蓝牙,Zigbee 模组时,由于本身功耗小,模组的供电电压会维持正常电压值比较长时间,不利于通过快速连续通断电来实现对模组配网信息进行重置。
为了改善上述问题,需优化供电方案。主功率线路与模组的供电线路需要通过二极管 D1 隔开,且主功率电容 C3 放在二极管的负极,同时 C1 和 C2 需要使用小容量电容。这样输入电压断电后,C1 和 C2 电容放电更快,模组端的 3.3V 电源引脚掉电也更快,可实现通过快速连续通断电实现对模组配网信息进行重置。由于断电后会出现 C3 电压高于 C2 电压的现象,所以阻隔二极管 D1 一般选择反向耐压高于 600V 的整流二极管。
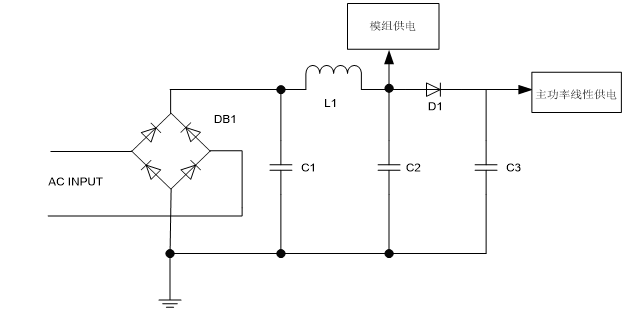
第二步 选择 LED 驱动电源方案
一路 AC-DC 恒流驱动调光方案
AC-DC 恒流驱动调光方案——开关电源方案
该方案中模组输出 PWM 信号。
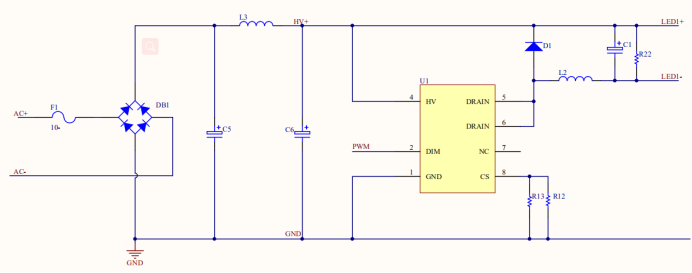
- 优点:效率高,PF 高。恒流特性好。线性度好。输出电压可调范围宽等等。
- 缺点:EMI 较差,成本高。PWM 调光有噪音。PCB 布局较难。
- 设计注意事项
- 因为 LED 驱动芯片集成高压 MOS,工作时,芯片本身发热量大,所以芯片的散热引脚的铜片面积尽量大,以减小热阻,增强散热能力。
- 芯片 DRAIN 引脚、电感引脚及二极管引脚间的走线尽可能短、宽。
- 从模组引脚到芯片引脚的 PWM 信号走线尽量短,避免 PCB 的其他噪声信号对 PWM 信号的干扰。
- 高压走线需要注意与低压走线的间距。
AC-DC 恒流驱动调光方案——线性方案
该方案中模组输出 PWM 信号。
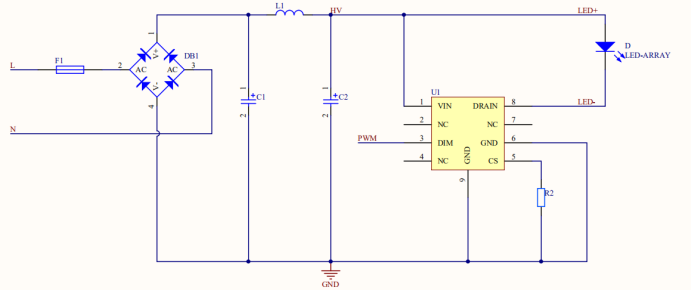
- 优点:成本低,无 EMI 问题,PCB 布局简单。PWM 调光无噪声。
- 缺点:效率低,窄电压范围恒流特性差。线性度差。输出电压固定等。难以实现高PF。
- 设计注意事项
- 因为 LED 驱动芯片集成高压 MOS,工作时,芯片本身发热量大,所以芯片的散热引脚的铜片面积尽量大,以减小热阻,增强散热能力。
- 从模组引脚到芯片引脚的 PWM 信号走线尽量短,避免 PCB 的其他噪声信号对 PWM 信号的干扰。
- 高压走线需要注意与低压走线的间距。
两路AC-DC恒流驱动调光方案
两路调光方案有两种控制方式,CW 和 CCT。
CW 是两路 PWM 信号,每路信号是混合控制亮度和色温的一种调光调色方式。两路信号分别为 CW 和 WW,其中 CW 控制白光(高色温),WW 控制暖光(低色温)。单路调光时使用 CW 控制信号。
CCT 为亮度和色温分别控制的一种实现方式,其中一路信号 Bright 控制亮度,一路信号 CCT 控制色温。
CW 控制 AC-DC恒流驱动方案开关电源方案
该方案下 CW 和 WW 是两路 PWM 信号,由模组输出。
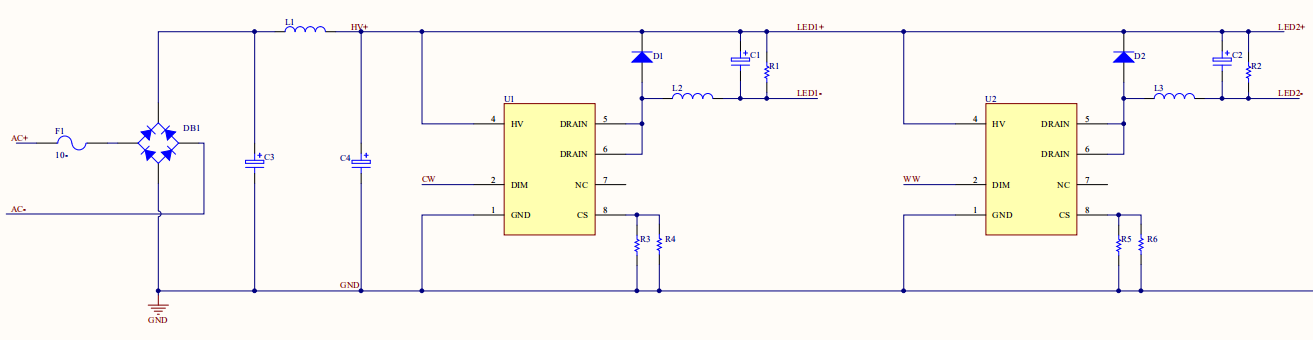
- 优点:效率高,恒流特性好,线性度高。调光效果好。
- 缺点:EMI 较差,电路有噪声,在小占空比下色温偏移比较严重。电路布局复杂,成本高。
- 设计注意事项
- 因为 LED 驱动芯片集成高压 MOS,工作时,芯片本身发热量大,所以芯片的散热引脚的铜片面积尽量大,以减小热阻,增强散热能力。
- 芯片 DRAIN 引脚、电感引脚及二极管引脚间的走线尽可能短、宽。
- 从模组引脚到芯片引脚的 PWM 信号走线尽量短,避免 PCB 的其他噪声信号对 PWM 信号的干扰。
- 高压走线需要注意与低压走线的间距。
CW 控制 AC-DC 恒流驱动方案
该方案下 CW 和 WW 是两路 PWM 信号,由模组输出。
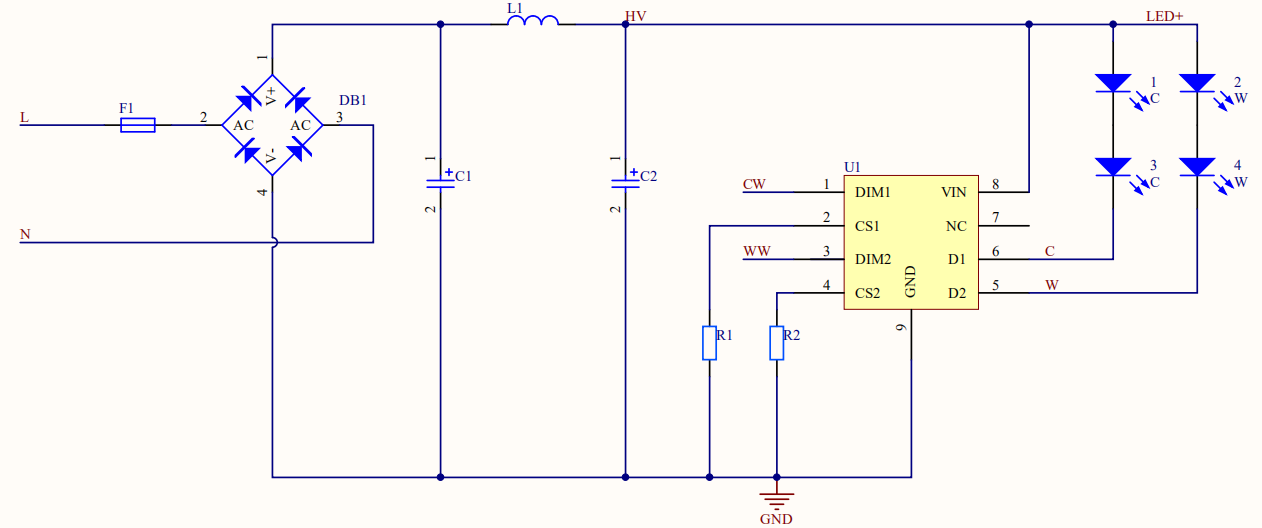
- 优点:成本低,无 EMI 问题,PCB 布局简单。PWM 调光无噪声。
- 缺点:效率低,窄电压范围恒流特性差。线性度差。输出电压固定,在小占空比下色温偏移比较严重等。
- 设计注意事项
- 因为 LED 驱动芯片集成高压 MOS,工作时,芯片本身发热量大,所以芯片的散热引脚的铜片面积尽量大,以减小热阻,增强散热能力。
- 从模组引脚到芯片引脚的 PWM 信号走线尽量短,避免 PCB 的其他噪声信号对 PWM 信号的干扰。
- 高压走线需要注意与低压走线的间距。
CCT 控制 AC-DC 恒流驱动方案
该方案下 Bright 和 CCT 是两路 PWM 信号,由模组输出。
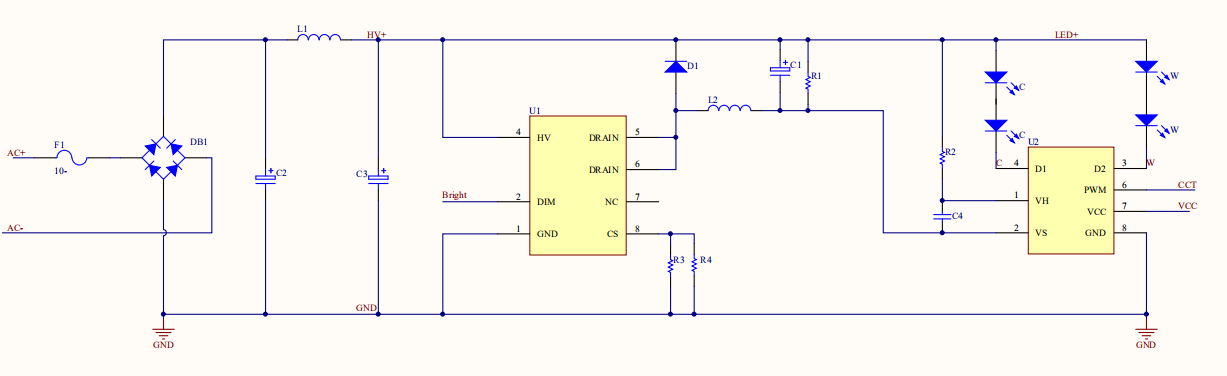
- 优点:效率高,恒流特性好,线性度高。调光效果好。亮度控制可以选择模拟方式,无噪音。
- 缺点:EMI 较差,色温偏移基本不变。电路布局相对简单,相比线性 CW 控制,成本高。
- 设计注意事项
- 因为LED驱动芯片集成高压 MOS,工作时,芯片本身发热量大,所以芯片的散热引脚的铜片面积尽量大,以减小热阻,增强散热能力。
- 从模组引脚到芯片引脚的PWM信号走线尽量短,避免 PCB 的其他噪声信号对 PWM 信号的干扰。
- 高压走线需要注意与低压走线的间距。
- 旁路电容 C1 选择低 ESR 的旁路电容,ESR 越大,效率损失会变大。
- 功率电感 L2 选择饱和电流必须比输出电流高 30%~50%。在电流能力满足要求的前提下,电感可稍取大些,这样恒流的效果更好。
- 为了保证最大的效率以及性能,二极管 D1 应选择快速恢复、低正向压降、低寄生电容、低漏电的肖特基二极管,电流能力以及耐压视具体的应用而定,但应保持 30% 的余量,有助于稳定可靠的工作。
注意:选择二极管时,需要考虑温度在 85°C 以下时二极管的反向电流能力。
- U1 的 DRAIN 脚处在快速开关的节点,所以 PCB 走线应当尽可能的短,另外芯片的 GND 端应保持尽量良好的接地。
- 尽量减小电流采样电阻 R3、R4 两端走线引起的寄生电感,以保证采样的精度。
- U2 的 D1、D2 引脚的铜箔面积要尽可能的大,以提高散热性能。
- 芯片引脚的旁路电容靠近引脚放置。
三路 RGB 驱动恒流调光方案
DC-DC PWM 控制线性恒流驱动
该方案中,模组输出 PWMR、PWMG、PWMB 三路 PWM 信号。线性恒流驱动可以实现 RGB 电流的恒定输出。
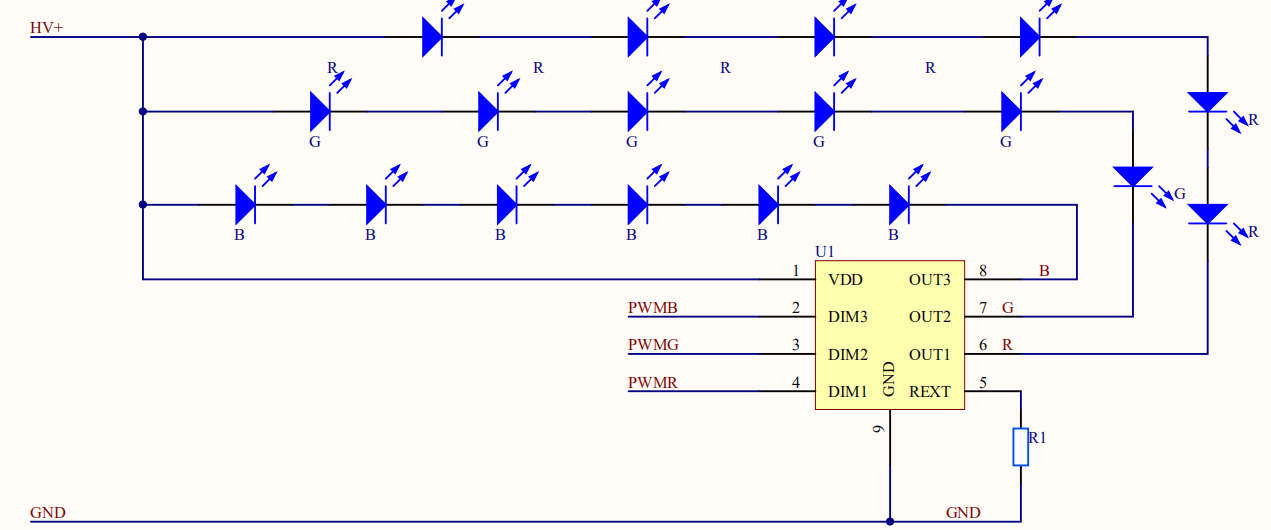
设计注意事项
- 因为LED驱动芯片集成高压MOS,工作时,芯片本身发热量大,所以芯片的散热引脚的铜片面积尽量大,以减小热阻,增强散热能力。
- 从模组引脚到芯片引脚的PWM信号走线尽量短,避免 PCB 的其他噪声信号对 PWM 信号的干扰。
- 高压走线需要注意与低压走线的间距。
DC-DC I2C 控制线性恒流驱动
该方案中,I2C 控制只需 DAT 和 CLK 两个信号即可实现对三路或者五路灯的控制,控制管脚相对较少,减少了模组管脚的负担。模组输出 DAT 和 CLK I2C 信号给驱动芯片从而控制 RGB 电流恒流。使用 I2C 方案控制需要注意 PCB 布局走线。
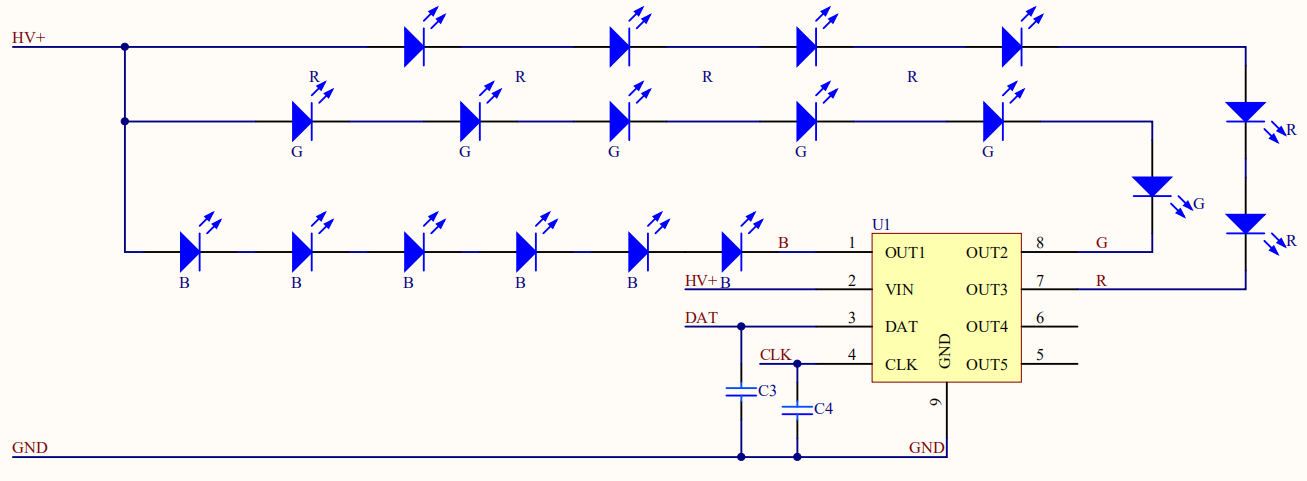
设计注意事项
- 因为 LED 驱动芯片集成高压 MOS,工作时,芯片本身发热量大,所以芯片的散热引脚的铜片面积尽量大,以减小热阻,增强散热能力。
- 高压走线需要注意与低压走线的间距。
- I2C 信号容易受到开关信号(来自 AC-DC 驱动电路)的干扰。如果干扰比较严重,可以考虑在 PCB 布局时 DAT 和 CLK 加滤波电容(10pf~50pf)做滤波来改善。
- I2C 信号需要在模组外围 DAT 和 CLK 信号上加上拉电阻,电阻阻值一般选择 4.7K(可根据实际应用选择)。
DC-DC PWM 控制 BJT/MOS 开关驱动
该方案使用 BJT 或者 MOS 通过 PWM 信号开关控制 RGB LED。RGB 不支持恒流,电流离散性较大。同样输入条件下,由于红光二极管电压低,需要在控制红光一路加电阻来限流,因此增加了不必要的损耗。注意灯珠电压与输入电压压差不要太大。
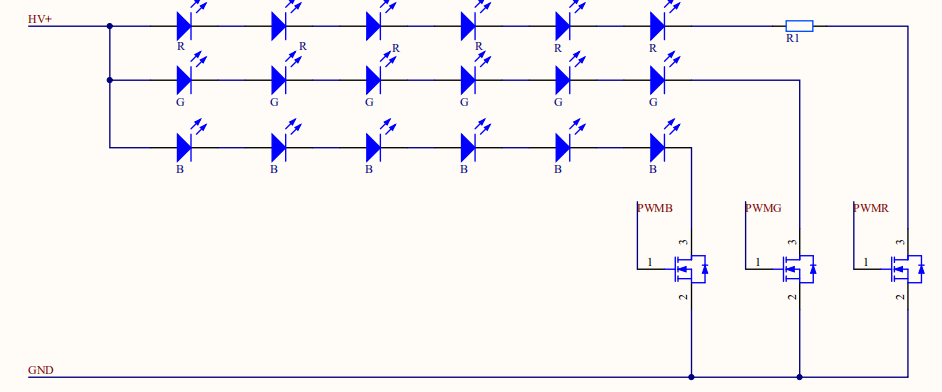
设计注意事项
- MOS 工作时,芯片本身发热量大,所以芯片的散热引脚的铜片面积尽量大,以减小热阻,增强散热能力。
- 高压走线需要注意与低压走线的间距。
- 从模组引脚到芯片引脚的PWM信号走线尽量短,避免 PCB 的其他噪声信号对 PWM 信号的干扰。
五路 AC-DC I2C 线性恒流驱动调光方案
该方案中 RGB 需单独供电。推荐使用 AC-DC 加 DC-DC 方案给模组供电。
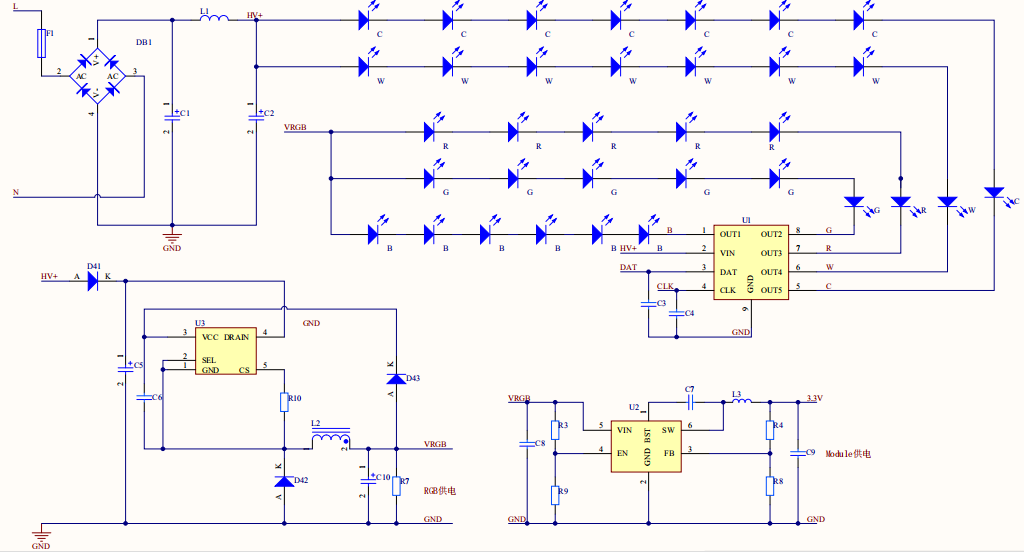
- 优点:方案简单,外围参数简单,成本低。控制只需 DAT 和 CLK 两个信号。
- 缺点:线性恒流驱动,DAT 和 CLK 信号容易被干扰。
- 设计注意事项
- 因为 LED 驱动芯片 U1 集成高压 MOS,工作时,芯片本身发热量大,所以芯片的散热引脚的铜片面积尽量大,以减小热阻,增强散热能力。
- 高压走线需要注意与低压走线的间距。
- I2C 信号容易受到开关信号(来自 AC-DC 驱动电路)的干扰。如果干扰比较严重,可以考虑在 PCB 布局时 DAT 和 CLK 加滤波电容(10pf-50pf)做滤波来改善。
- I2C 信号需要在模组外围 DAT 和 CLK 信号上加上拉电阻。电阻阻值一般选择 4.7K(可根据实际应用选择)。
- AC-DC 恒压电路设计可参考 电源设计 文档,了解相关注意点。
- 基于DC-DC转换芯片设计的buck电路,需要注意两个主功率环路面积尽量小。
- 环路1:C8 正极 > U2 > L3 > C9 正极 > C9 负极 > C8 负极。
- 环路2:U2 SW引脚 > L3 > C9 正极 > C9 负极 > U2 GND 引脚。
- 基于 DC-DC 转换芯片设计的 Buck 电路,需要注意反馈电阻靠近芯片引脚放置,芯片引脚的滤波电容靠近芯片引脚放置。